Architectural Grade | Top quality log and veneer length over 2.65m. |
Architectural Grade | Top quality log and veneer length over 2.65m. |
Backing | The lowest grade veneer which is generally only used yet as crossband veneers or for non-visible surfaces. |
Backing Board | The boards which remain after slicing wood. |
Birds-eye | The term given to eye-shaped marking of the veneer, especially in the case of Birds-eye Maple. |
Block Mottle | An irregular form of figuring which runs over the complete surface of the veneer. |
Blue Stain | Blue stains on the surface of the veneer which occur through insufficient water extraction when slicing (too low heating capacity on the pressure bar or when slicing too fast) because water remaining on the surface of the veneer turns blue through oxidation. |
Book Matching | This traditional method of matching is achieved by taking successive leaves of veneer and reversing each alternate leaf so as to bring corresponding opposite edges together in a mirrored effect. This produces a symmetrical balanced pattern of grain and figure. 
|
Buckle | Corrugation caused in the veneer leaf when drying as a result of different drying runs and irregular annual ring development within the veneer leaf. |
Bundle | Cut bundles of veneer generally containing 24 or 32 consecutive leaves in cutting sequence. |
Burrs (burls) | A term for veneers which are produced from the burr or burl formation. Differentiation is generally made between burl or burr growth above ground (Elm, Ash, Oak) and root burl or burr growth which develops below ground in the root (Californian Walnut, Madrona, Vavona, Myrtle). |
Butt | The bottom end of a log or veneer frequently featuring coarse annual ring development and undesired colour variations caused by rootstock. |
Cathedral | Much sought after structure in crown cut bundles. Considered to be among the most attractive veneers. |
Chatter marks | Caused through vibration of the veneer block on the slicing machine or by wrong pressure setting on the machine, showing on the veneer leaf as regularly distributed cross running strips. The veneer block vibrates when the log is not firmly clamped flat on the cutting table. |
Clipping | The clipping of veneers on the veneer cutter whether the veneers are in their initial or in final production. |
Complete Flitch | Veneers which are produced from one log and where all leaves remain in their exact original log sequence. |
Condensate | The tannic acid which is yellow in colour and deposits on the surface of the veneer when it is dried too sharply. |
Crown cut | The first bundles from a log when sliced over the heart. Produces the so-called cathedral structure. 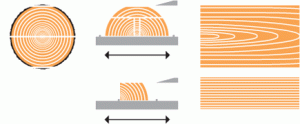
|
Curl | Curl veneer figuring sometimes termed “crotch” which is manufactured from the intersection of the limb or branch with the main trunk. 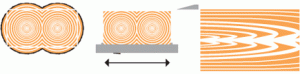
|
Discolouration | Undesirable colour variations in the veneer. |
Divider | A strip of wood placed between the veneers to increase the strength of a pallet to ensure the stability of the flitches stacked in log-form. Also separates the different logs from each other. |
Door Length | Log and veneer lengths between 2.05m and 2.40m required by the door industry. |
Drier Prints | Black patches are given on the surface of the veneer caused by defective, uncleaned or un serviced drier belts. These black patches cause problems when sanding and treating the surface of the veneers. |
Fiddle, Fiddleback, Figure | Clearly visible and more or less regular streaks running across the grain in different species of wood (e.g. in Sycamore, Makore, Maple. Anegre, Peartree, Ash). The more regular these streaks are the more valuable the veneer. |
Flake | The typical figuring of wood when the pith rays are cut across, i.e. at an angle of 180 degrees when slicing. This is particularly strongly pronounced in Oak. Desired in veneers such as Plane Tree. |
Flares | Irregular veneer marking. |
Flat Cut | A veneer slicing technique. 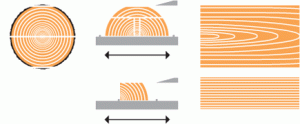
|
Flitch | Log-end. |
Flitch Stock | Complete flitch. |
Furniture Grade | Veneer differing in length from 1.00m to 4.00m within one log which can be worked by the furniture industry. |
Grading | Quality-related grading of veneers and the pricing of the various grades. |
Grading price | Price determination for a veneer log. |
Gum | Black spots or patches which can occur in Black Cherry veneer. They are not arranged in a regular pattern and occur in different positions from one veneer leaf to the next. |
Heart | The term used for the core wood area in veneer which is different in colour to the remaining part of the veneer leaf. |
Horizontal Slicer | A slicing machine on which the counter movements of the log and knife are horizontal. |
In Bark, Ingrown Bark | Bark occurring in burl or burr logs within the heart wood which as been overgrown. |
Jet Drier | Veneer drying machine which dries the veneer in a continuous operation using hot air. |
Layons | Leaves of veneer jointed together to form a sheet with specific dimensions. |
Leaf | Veneer leaf. |
Light Scratch | Very fine knife scratch which disappears from the veneer when the surface is sanded and as a result does not degrade the veneer. |
Log | The section of a tree that can be sawn or used for veneer. |
Log Run parcel | A completely converted log parcel which is offered and sold as veneer with all its grades included in it. |
Log-end Flitch | Term used for a log or part of a log or veneer form. |
Lumber | Already converted solid wood. |
Lumber Logs | Sawing quality logs. |
Matching | Veneer leaves are stored in the sequence of cutting, enabling leaves to be selected and matched as required. Each leaf is subtly different but related to the adjacent leaves, so that different forms of matching can be achieved. The gradual variation of grain through the log gives veneers their special quality of subtle variations. Because of the variation, and because the size of leaves is obviously limited by the size of log, the selection and matching of veneers for each job is critical. The art of veneer matching is to make use of the natural repeat of the grain of the wood from leaf to leaf to arrange the leaves or slices of veneer to form a variety of different decorative patterns and effects in keeping with the grain characteristics of the particular species. |
Mild Texture | Very fine and slow growing wood which produces a beautiful, even marking in veneer. |
Minerals | Dark patches or pockets of wood, especially occurring in the American Oak. |
Mismatching | Leaves from one log are deliberately mixed to give a random planking effect whilst maintaining an overall consistent grain and colour. 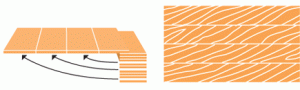
|
Miss-cut | Veneer defect caused in the processing, generally leading to fluctuating veneer thicknesses. |
Number of Leaves | The number of leaves in a bundle; generally 24 or 32 leaves. |
Open Defect | Faults in veneer which produce holes. |
Panel Length | Log and veneer lengths between 2.50m and 3.40m required by the panelling industry. |
Parcel | A quantity of veneer prepared for the customer, often sorted into uniform qualities. |
Pommele | Comes from the French word Pommele, meaning Apple. The term given to a regular veneer marking which resembles apples. |
Press Drier | In this equipment the veneers are pressed between large rotating drums in addition to running through the jet drier to avoid waviness. |
Pressure bar | The bar opposite the knife. The gap between the knife and pressure bar is slightly narrower than the thickness of the veneer to generate the necessary counter-pressure for a smooth cut. |
Quarter Cut | A veneer slicing technique. 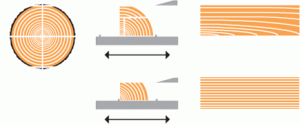
|
Quarter Matching | This is a traditional way of jointing veneers based on the nature of the growth of the tree from which the veneers are cut. A veneered panel is made up from four pieces which are book matched both from side to side and from top to bottom. This method is useful in making up larger panels and when using species where only small leaves are available. It would normally be applied to butts, burrs and curls. 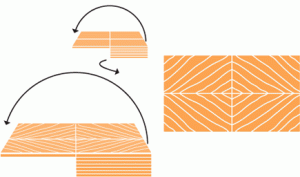
|
Quartered | Conversion of veneer logs which have been quartered. Produces quarters and half crowns. |
Quarters | The bundles from a log which are given after opening the flitch (and, sometimes, cutting out of the heart) where the annual rings are cut radially at an angle of 90 degrees by the knife. Typical stripy structure of the veneer. |
Quartier | It produces half crown and quarters. |
Random Matching | Veneers of the same species, but not necessarily from the same log, are deliberately mixed and mismatched to produce an overall grain effect with no particular pattern. Butt or end grain jointing may be introduced in some leaves to add to the planking effect. 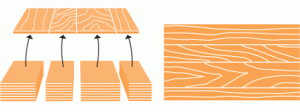
|
Resin Pockets | Resin pockets in softwood which produce holes in the veneer and are thus degrading. |
Rift | Quartered veneer flitches converted on the stay-log machine thus resulting in broad quarters being in sequence. |
Rift Cut, Also Faux Quartier | Quartered flitches which are sliced on the knife in a normal way. 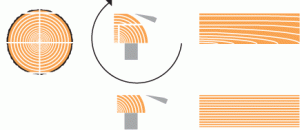
|
Rotary Cut | Veneer cutting machine on which the log is clamped centrally when brought up to the knife while rotating so that the veneer leaves are peeled off spirally. Used for almost all burr veneers, Birdseye Maple or Birch. 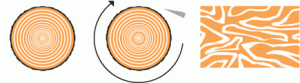
|
Rough Cut | When slicing veneers rough patches are caused in the surface because of bad clamping of the log, setting the machine wrongly or by too strong fluctuations in texture. The cause can also be that the flitch is not hot enough when cut. |
Sap | The outer cell layer of the wood between bark and heartwood. The supply of water and nutrients to the tree is only through the outer row of sap cells. The remaining layers of cells in the sapwood is cut away in most veneers. |
Scratch | A notch which runs across the veneer leaf caused by a faulty knife. |
Sequence | The sequence of veneer leaves within a bundle and the complete log. |
Shake | Cracks in the lumber which follow the course of the annual rings. Part of trunks with this defect are not suitable for producing veneer or sawn timber. |
Short Length | Log and veneer between 0.80m and 2.00m in length. |
Single Bundles | Bundles of veneer taken out of their regular sequence within the log so that the sequence is no longer given. |
Slip matching | Successive leaves are taken from the same stock or flitch of veneer and jointed without turning alternate leaves over as in book matching. This produces a repeat pattern which varies gradually across the panel. This method is usually most effective when straight grain veneers are used. 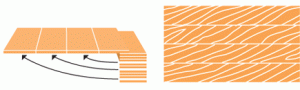
|
Stacked in Log Form | The presentation of veneers stacked in their original log form. |
Starter Bundles | The first bundle cut from a log. |
Stay-Log | Special veneer cutting machine in which the line of cut sweeps across the growth rings in a circular direction to give eccentric cutting. |
Tension | Differences in density occur in a trunk though different growth zones and growth speeds (weather side) which can lead to tension in the log. When a tree is felled cracking as a result of tension can occur making its use as veneer questionable. Problem especially with Beech. |
Thick Cut | Veneers which are produced in other thicknesses. Usual thicknesses are 1.2mm, 1.5mm and 2.5mm. Larger thicknesses are usually produced as sawn veneers, i.e. cut on the block bandsaw. |
Top Grade Log | Used to express a particularly high quality of a log. |
True Quarter Cut | The cutting of the log into four quarters. In the case of Oak this gives a higher portion of veneers with fine flakes. However, the yield is generally smaller than when converting in other ways. 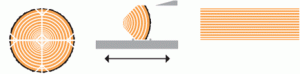
|
Turning Veneers | The presentation of a log which is shown bundle by bundle. |
Vat | The pit used for steaming or cooking logs. Earlier it used to be brick-built, today such vats are generally lined with steel or aluminium to make the pit more durable. |
Vertical Slicer | Vertical slicer on which the log and knife counter movements are carried out vertically. |